7. Deck hand |
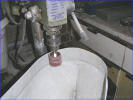 |
Over to Bradders for
an update on the hull....
"Well I received the hull in good shape despite Martin's best efforts!
After reading the instructions the suggestion is to sand the rough
fibreglass inner bulwark edges after the deck had been installed but I
thought this would be simpler to do beforehand.
|
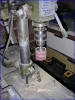 |
I used a sanding drum in the pillar drill with a 'medium' grade drum which
smoothed the inner edges effortlessly. |
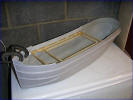 |
The frame is the
first thing to go in the hull - the position is measured from the top edge
of the bulwark down (I used a piece of scrap wood as a gauge and drew a
pencil line). After marking out I believe the deck is about 5mm higher than it should be i.e. the angle iron
pieces that go on to the inner edge of the deck are actually in the wrong
place compared to the outside rubbing strip detail, but I decided to go
with the instructions.
|
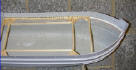 |
The top surface of the two outer
'longerons' of the frame needs lots of little saw cuts made in the top of them.
this allows the frame to be bent upwards at each end making the deck SLIGHTLY concave
(about a 6mm 'dip' in the middle). I Glued with 5 Min epoxy using lots of clamps. be careful not to damage the outside of
the hull.
|
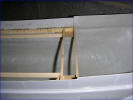 |
I found a discrepancy in the
instructions when aligning up the frame in the hull, the measurement
from the stern to the frame is 270mm but this would leave the Bulkhead 'J'
hanging in mid air, I reckon the measurement is nearer 260mm.
(I panicked a bit here as Martin had
made the frame and I feared the worst !!!!)
|
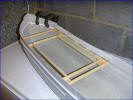 |
Next the front deck
supports. These are made of plastic and were glued in with 5 min epoxy for
the first one and the second lamination superglued to the first. I had
difficulty understanding where the position of these should be in relation
to the bulwark to edge and after some thought these should follow the
position of the strake on the outer hull (well that where ours went !) |
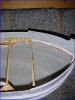 |
After all of the bits were glued in
position I ran a fillet of car body filler around the underside of the
supports just to create a stronger joint. (the more filler now...the less
ballast later... !). |
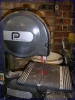 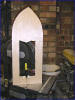 |
The main deck is
next cut out on my trusty band saw. I cut an entrance through the rear
section and cut out the centre. I just glued a piece of scrap over
the initial entrance cut and will sort this out later.
|
 |
Some cutting and trimming is need
to make this deck fit where is should into the hull as, the pre-penned in
outline is a very rough guide. (This looks like martin has had a go at it
:o) |
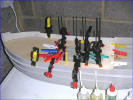 |
Once the deck is trimmed to size it can
be glued down to the frame with PVA glue and epoxy to the hull.... and
Lots clamps! |
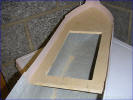 |
With the deck in place, the bulwarks
were skimmed with an initial layer of car body filler. |
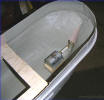 |
The prop tube was installed at this
point -
("Bit out of sequence there mate!" - Martin ).
A wooden platform was made up to the dimensions of the polystyrene
block rigid coupling connected and the everything lined up. |
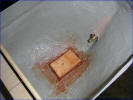 |
Once aligned, the prop tube was epoxied
in and a support fillet of filler applied. The motor mount was also glued
down and a patch of glass fibre matting applied over the top to doubly
reinforce it. |
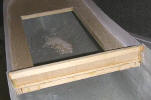 |
Stern bulkhead plate next.
Cut out and trim to size. Liberal amounts of epoxy with avoid the need for
the two countersunk screws through the hull!!!!?! |
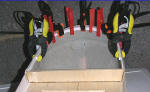 |
The quarter deck supports going in.
Remember the quarter deck fit flush with the hull. |
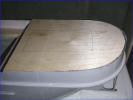 |
Test fitting of the quarter deck. As you can see, quite a bit of filling
to do! |
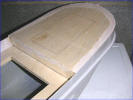 |
Don't worry about the filler, this deck is meant to be metal, the printed
wooded fits on top. |
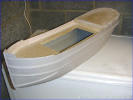 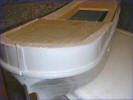
Filling the gaps and sanding down.
Notice I haven't cut out the access hatch yet... (Yes I
had!?! - Martin )
This is because the hole will be made to the cabin superstructure size of
which Martin still has (Ah! Ok - Martin). |
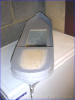 |
Test priming the hull to see how much extra filling and sanding need to be
done." |
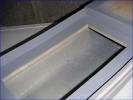 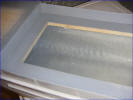 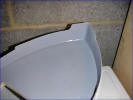 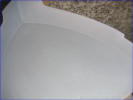
Looks pretty good to me! |
Well all this just my opinion, but what do I
know!
|
Home
|