Meanwhile...
in this thread:
https://www.modelboatmayhem.co.uk/forum/index.php/topic,70510.0.html I described the modification from gas phase feed to liquid phase feed.
This mod allowed more fuel to the boiler, and since back then when the steamplant was initially commissioned, the throttle valve was basically adjusted to what the burner could deliver, it stood to reason that this adjustment also was reviewed.
Alas, more fire, more steam to the engine, what is not to like?
Well, this: it turned out that the oil separator, which could keep up in the previous situation, now could not anymore. Oil passed the separator and ended up in the condensat return. Dammit!
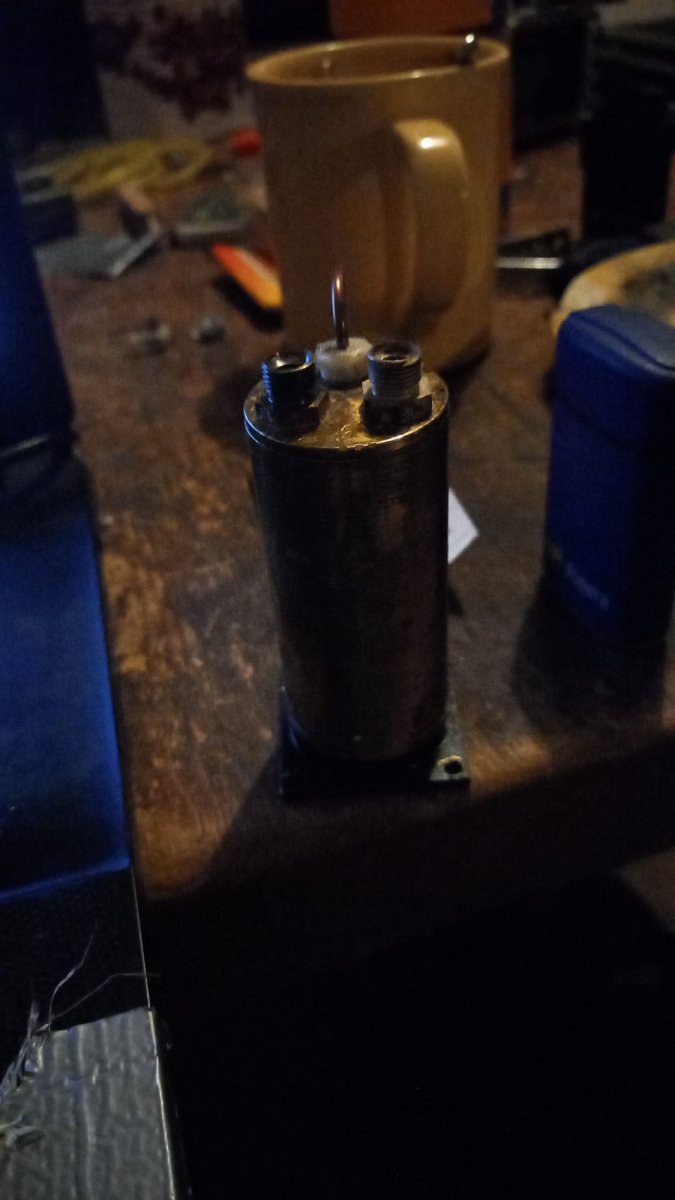
This beautiful piece of equipment is the oil separator. It is a very simple drum, with exhaust steam inlet, and clean steam outlet on the top. The idea is that oil and emulsified droplets of condensate fall to the bottom, and clean steam escapes. Right side is dirty steam in, left side is the clean steam out. In the background the riserpipe that discharges the collected crud.
Back before the mod, this would work until full throttle, and after the mod, it still worked flawless up to about 75% throttle (basically equivalent to the pre-mod full throttle).
What was happening? The only thing I could think of, was that higher throughput, would also increase the velocity of the dirty steam into the separator.
This steam is jetting vertically downwards, and down there at the bottom is a puddle of crud. Increased velocity could mean that the incoming steam would whip that puddle into a froth, throwing droplets around, and thse droplets could then be "sucked up" by the equally increased velocity with which the (now not so) clean steam leaves the separator.
My solution:

I soldered a 5 mm ID tube at the bottom of the inlet connection. This tube has an open end, but is measured to exactly end up at the bottom of the separator vessel, so practically, this end is closed off. Mind you, NOT "sealed off", meaning any liquid (oil or emulsified water) inside that inlet diverter pipe can flow out through the seams, but steam won't blow into the puddle of crud and whip it up.
In the side, 5 holes 2 mm crossection are drilled, and they are indexed such that the steam in the separatorvessel gets a counterclockwise rotation. This rotation should help any droplet of liquid to find the outer wall, cling to it and flow down. The 5 holes should be sufficient to reduce steam velocity, in order to reduce/eliminate any possible frothing.
So now we have a (relatively slowly) rotating body of steam in the separator vessel, centrifuging out any droplets, the liquid flinging to the wall and flowing down, clean and moisture free steam rising to the top of the vessel and escaping to the condenser. Or at least, that is the expectation.
I fired up the boiler, and once hot, set the throttle to full speed and left it running for a full tank of fuel.
What I noticed was that initially there was a bit of turbidity of the condensate (which of course was not the funniest of observations, to put it mildly), but this seemed to clear within 5 minutes. I think I was looking at "old oil" in the condenser left there by previous sessions.
Also, I had the clear impression that the amount of liquid discharged by the separator was less than usual, and also the properties of that effluent had changed: it was oil and water like before, but previously, that water was very strongly emulsified, now it appeared much clearer. I cannot explain the reduction in volume, but I think the reduced emulsifying is due to the reduction in velocities inside the separator vessel.
All in all, I'm happy...
I've got more power, and I can practically use it now too.
EDIT: final report, I checked the water in the Hotwell, and found an ever so slight turbidity, barely visible. I think this was residual from the dirty shot of water in the first 5 minutes, and should not return anymore. It was anyway so minor that I don't think this will cause any problems.